PAM-RTM - Basic Training
Be able to model, analyze results and optimize through simulation residual stresses and resulting geometrical distortions. Be able to identify required data and to determine proper assumptions for simulations.
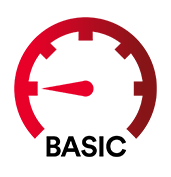
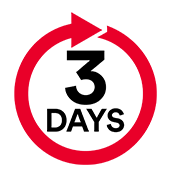
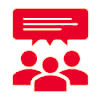
Audience
CAE engineers, Process engineers, Material engineers, Designers
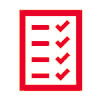
Prerequisites
Basic FEA knowledge and basic composites material knowledge
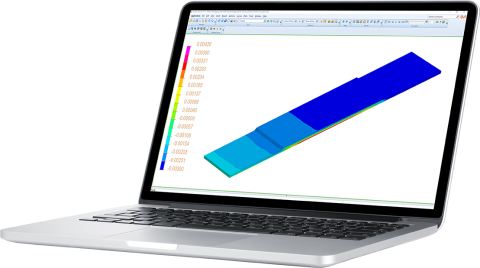
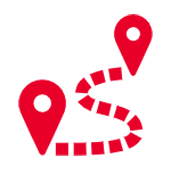
LEARNING PATH
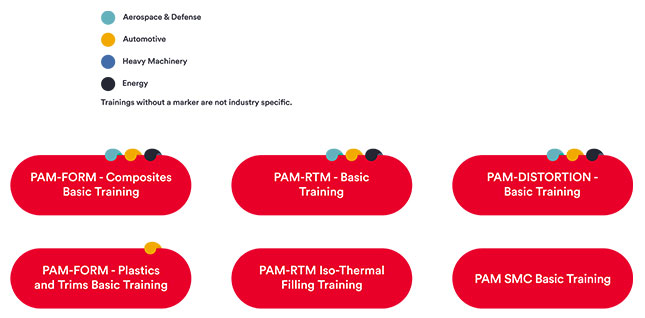
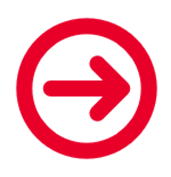
SUGGESTED COURSES
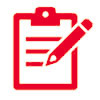
DESCRIPTION
This training is meant for engineers responsible for designing curing processes of composite parts. This training relies on PowerPoint presentation and practical use cases executed on workstation. This training will allow the trainee to confidently create simulation models.
No suitable date or place?
Set up a private training
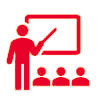
TRAINING PROGRAM
Day 1 – Physics and GUI Description
- Introduction on physics, modeling, material requirements
- GUI description and workflow Visual-RTM and Visual-Viewer
- Shell model simulations: From CAD (1) to simulation with simple tutorials.:
- Vents, air traps, gravity effect.
- Permeability and fiber orientation definition.
- Layer design manager.
- Channels and runners.
- Automatic process: Triggers and sensors.
Day 2 – Isothermal Analysis
- Shell model for injection simulation: Options of filling simulation
- Air entrapment, gravity
- Solid model simulations
- From CAD (1) to simulation with advanced tutorials.
- CPD and lay-up importation.
- Mesh of a complex laminates. Automatic mesh.
- Coupled thermal and curing simulations: Preheating, Heated RTM and Curing
(1) This training course includes initiation to Visual-Mesh regarding the specific meshing needs of the treated models. However, it does not include a complete Visual-Mesh training that can be ordered separately.
Day 3 – Draping effect, Non-Isothermal and Fluid-Mechanic analysis
- Solid model simulation with thermal analysis
- Coupled thermal and curing simulations: Mold preheating, Heated RTM and Curing
- Effect of draping on injection (Importation of fiber direction and laminates):
- Link with QUIKFORM on shell and solid model
- Link with PAM-FORM on shell and solid model
- Extra options: Flow optimization, porosity, overfilling and gravity
- Fluid-mechanic simulations: Infusion, Core deformation, Light-RTM and CRTM